Top 4 FAQs About Rotogravure Printing
Date: Apr 30 2025 From: Star Color Views:
Rotogravure printing is a highly efficient and high-quality printing method widely used in packaging production for industries such as food, pharmaceuticals, and daily chemicals. Despite its mature technology, practical production still faces challenges like registration deviation, ink atomization, color difference, and excessive solvent residue. These issues not only affect product quality but also increase production costs, hindering business growth. With over a decade of experience in the printing industry, the author analyzes how to address these problems below.
1. Excessive Registration Deviation (>0.15mm)
Phenomenon and Impact
Registration deviation is a common and critical issue in rotogravure printing. When the deviation exceeds 0.15mm, patterns and text on printed materials fail to overlap accurately, causing defects like ghosting and white spacing. This severely impacts the aesthetics and readability of products, especially problematic for packaging where clear information is essential.
Causes and Solutions
Registration deviation stems from multiple factors, but optimizing traditional parameters and adopting advanced technologies can significantly reduce errors:
- Substrate Tension Fluctuation: Traditional tension control allows fluctuations of ±5N, causing substrate stretching or shrinking. Upgrading to a closed-loop servo control system (±0.8N) ensures real-time tension monitoring and adjustment, stabilizing the substrate and reducing registration error to ≤0.08mm.
- Temperature Difference of Guide Rolls: A temperature gap of 3–5℃ between guide rolls creates thermal expansion differences in the substrate. Implementing a zoned thermostatic system (±0.5℃) reduces thermal expansion impact by 72%.
- Plate Cylinder Machining Precision: Traditional plate cylinders with 0.02mm concentricity struggle with high-precision printing. Laser engraving combined with dynamic balance correction improves concentricity, achieving radial runout ≤8μm for stable high-speed rotation and minimized deviation.
Smart Tool Applications
Intelligent tools play a key role in solving registration issues. The BST tension sensor (0.1N precision) monitors substrate tension in real time, while vision inspection systems (e.g., Keyence CV-X series with 0.01mm resolution) quickly detect deviations and feed data to the control system for automatic adjustments, enabling intelligent precision control.
2. Ink Atomization (Fly Ink) Pollution
Pollution Indicators and Risks
Ink atomization is a critical concern. When workshop PM2.5 concentration exceeds 35μg/m³ or ink droplets exceed 15μm in diameter, intervention is necessary. Fly ink pollutes equipment and the work environment, wastes ink, and poses health risks to operators over time.
Control Strategies
- Ink Rheology Modification: Adding 0.3% fumed silica (Evonik AEROSIL® 200) improves ink cohesion, reducing atomization. Controlling viscosity at 22±1s (No.4 cup, 25℃) stabilizes ink transfer and atomization behavior.
- Static Elimination System: Installing 3M 795 ionization bars (balance voltage ≤±50V) neutralizes static charges on ink and substrates. Maintaining environmental humidity at 55±5% RH further reduces static buildup.
- Equipment Modification: Enclosed doctor blade chambers with negative pressure (-10Pa~-15Pa) trap flying ink droplets, preventing environmental contamination. Adjusting the ink guide roller speed ratio from 1:1.1 to 1:1.03 optimizes ink transfer and minimizes atomization.
3. Printing Color Difference (ΔE >1.5)
Impact and Standards
Color difference directly affects product consistency and brand image. A ΔE >1.5 is visually detectable, unacceptable for color-sensitive packaging. Controlling color difference within tight ranges is paramount.
Full-Process Control System
- Ink Transfer Rate: Traditional mesh depth fluctuations (±3μm) cause inconsistent ink transfer. Laser engraving technology (±0.5μm precision) stabilizes transfer, limiting color density fluctuation to ≤0.05.
- Drying Uniformity: Oven temperature variations (±8℃) lead to uneven drying. Porous air nozzles combined with computational fluid dynamics (CFD) optimization reduce temperature differences to ΔT≤1.5℃, ensuring consistent color development.
- Online Detection: Manual sampling is slow and error-prone. The X-Rite IntelliTrax2 system provides real-time color monitoring, controlling ΔE ≤0.8 and triggering automatic parameter adjustments for deviations.
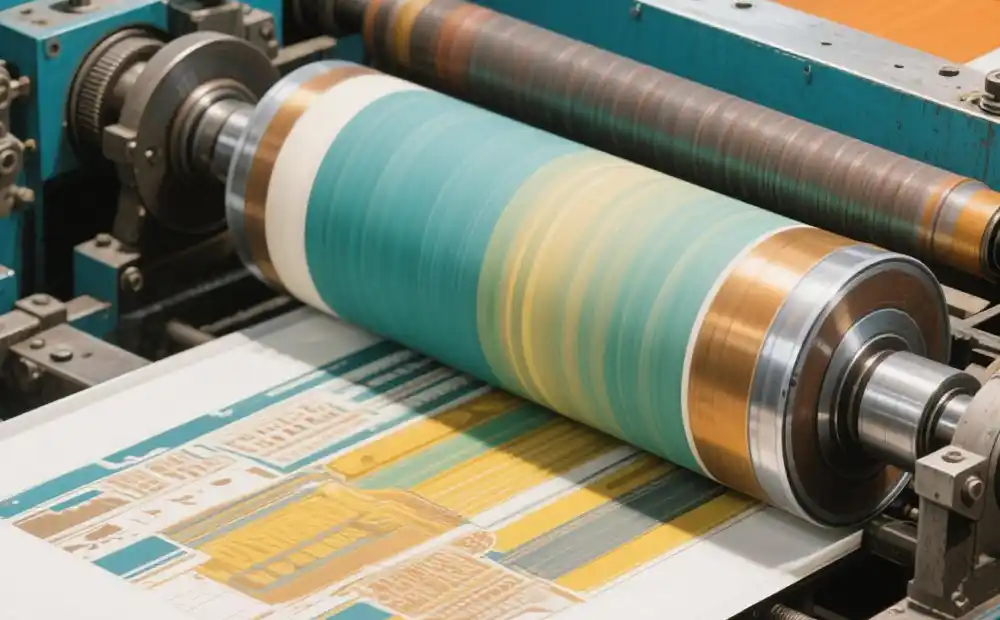
4. Excessive Solvent Residue (>5mg/㎡)
Risks and Standards
Excessive solvent residue threatens product safety and environmental health, especially for food and pharmaceutical packaging where harmful substance migration poses risks. The industry standard requires solvent residue ≤5mg/㎡.
Comprehensive Solutions
- Process Optimization: Gradient drying (60℃→85℃→105℃, with wind speeds 15/20/18m/s) ensures stepwise solvent evaporation. Extending the drying path by 1.2m per color unit enhances solvent removal efficiency.
- Material Upgrades: Low-residue polyurethane inks (Dow Enlight™) and high-Tg resins (BASF Joncryl®) minimize solvent retention, reducing inherent residue risks.
- Testing and Certification: Equipping PerkinElmer Clarus 690 gas chromatographs enables precise residue measurement. Obtaining ISO 15318:2023 certification ensures compliance with international safety standards.
By addressing these four key challenges with targeted solutions, enterprises can resolve practical production issues, improve product quality and efficiency, cut costs, and gain a competitive edge in the market.
For more insights on rotogravure printing, contact us at: eva@starcolor-ink.com