In-depth Guide to Gravure Roll Cleaning
Date: Apr 28 2025 From: Star Color Views:
The cleanliness of gravure rolls directly determines the quality of printed products, color reproducibility, and production efficiency. With the continuous increase in market requirements for printing quality, the cleaning technology of gravure rolls has also become a crucial aspect for enterprises to enhance their competitiveness. This article will provide an in-depth analysis of the core indicators of gravure roll cleaning and six major cleaning technologies, helping enterprises achieve efficient and precise cleaning of gravure rolls and reduce production losses.
I. Core Indicators of Cleaning Efficiency
To measure the cleaning effect of gravure rolls, quantitative evaluation is required from multiple dimensions. The following are the key indicators and compliance requirements recognized by the industry:
Parameter |
Industry Standard |
Compliance Requirement |
Cell Residue |
≤0.8mg/㎡ |
≤0.3mg for copper rolls |
Surface Roughness Ra |
≤0.2μm |
≤0.15μm for chrome-plated rolls |
Solvent Residue |
≤50ppm |
≤10ppm for food packaging |
Cleaning Cycle |
≤35 minutes per time |
≥400m/min for high-speed lines |
The cell residue is a key factor affecting printing quality. Residual ink or impurities can lead to issues such as blurred printed patterns and color differences. Professional analyzers can accurately detect the content of residual substances in the cells. For copper rolls, the residue is required to be ≤0.3mg to ensure the quality of printed products. For chrome-plated rolls, the surface roughness Ra should be controlled at ≤0.15μm.
In the field of food packaging printing, the requirements for solvent residues are even more stringent, with a limit of ≤10ppm to prevent the migration of harmful substances into food. The cleaning cycle directly impacts production efficiency. On high-speed production lines (≥400m/min), the cleaning cycle is required to be ≤35 minutes per time to minimize equipment downtime.
According to the 2023 industry report released by the China Printing Association, the use of scientific cleaning methods can extend the lifespan of gravure rolls by 40%, saving an average of $20,000 per device per year.
II. Comparison of Six Major Cleaning Technologies
Currently, the mainstream gravure roll cleaning technologies on the market each have their own advantages and disadvantages and are suitable for different application scenarios. The following is a detailed comparison of the six major cleaning technologies:
Method |
Applicable Scenarios |
Cleaning Efficiency Improvement |
Environmental Friendliness |
Ultrasonic Cleaning |
Gravure rolls with fine graphics |
92% |
Wastewater treatment required |
CO₂ Dry Ice Cleaning |
On-line quick cleaning |
85% |
Zero chemical pollution |
Laser Cleaning |
Stubborn resin residues |
97% |
No consumables |
Chemical Soaking |
Routine ink cleaning |
78% |
High VOC emissions |
High-pressure Water Jet Cleaning |
Large metal gravure rolls |
80% |
Water circulation system |
Plasma Cleaning |
Nanoscale cells |
89% |
Low energy consumption |
2.1 Ultrasonic Cleaning
Ultrasonic cleaning uses the cavitation effect generated by high-frequency vibrations to shatter and peel off the dirt in the cells, making it suitable for cleaning gravure rolls with fine graphics. Its cleaning efficiency can be increased to 92%, effectively removing ink residues in small cells. However, this method has a relatively high equipment cost, ranging from $30,000 to $70,000. Additionally, wastewater is generated during the cleaning process, requiring a dedicated wastewater treatment system to meet environmental protection requirements.
2.2 CO₂ Dry Ice Cleaning
CO₂ dry ice cleaning involves ejecting solid dry ice particles. Utilizing the principle of heat absorption during dry ice sublimation, it cools and embrittles the dirt, causing it to fall off. This method is especially suitable for on-line quick cleaning. It can rapidly clean the surface and cells of gravure rolls without interrupting the production line, with a cleaning efficiency improvement of up to 85%. The equipment cost is relatively low, starting from $10,000, and the cleaning process is free of chemical pollution, conforming to the concept of green production.
2.3 Laser Cleaning
Laser cleaning uses high-energy laser beams to irradiate the dirt, causing it to vaporize or peel off instantly. It has an excellent cleaning effect on stubborn resin residues, with a cleaning efficiency that can reach as high as 97%. However, the equipment cost for this technology is extremely high, exceeding $70,000. Despite the high cost, its advantages of no consumables and high cleaning efficiency make it irreplaceable when dealing with difficult cleaning tasks.
2.4 Chemical Soaking
Chemical soaking is a traditional cleaning method. By soaking the gravure roll in a cleaning agent, chemical reactions between the cleaning agent and the dirt are utilized to achieve the cleaning purpose. This method is suitable for routine ink cleaning, with a cleaning efficiency improvement of 78%. The equipment cost is relatively low, costing less than $10,000. However, this method generates a large amount of volatile organic compounds (VOCs), posing certain risks to the environment and the health of operators. Therefore, a complete ventilation and waste gas treatment system is required.
2.5 High-pressure Water Jet Cleaning
High-pressure water jet cleaning uses the impact force of high-pressure water flow to wash away the dirt from the surface and cells of gravure rolls. It is suitable for cleaning large metal gravure rolls, with a cleaning efficiency improvement of up to 80%. The equipment cost is approximately $15,000. Through a water circulation system, the reuse of water resources can be achieved, reducing cleaning costs and water waste.
2.6 Plasma Cleaning
Plasma cleaning achieves deep cleaning of nanoscale cells by generating plasma to chemically react with the dirt, with a cleaning efficiency improvement of up to 89%. This technology has low energy consumption, with an equipment cost of $40,000. It performs exceptionally well when handling high-precision and high-requirement gravure roll cleaning tasks.
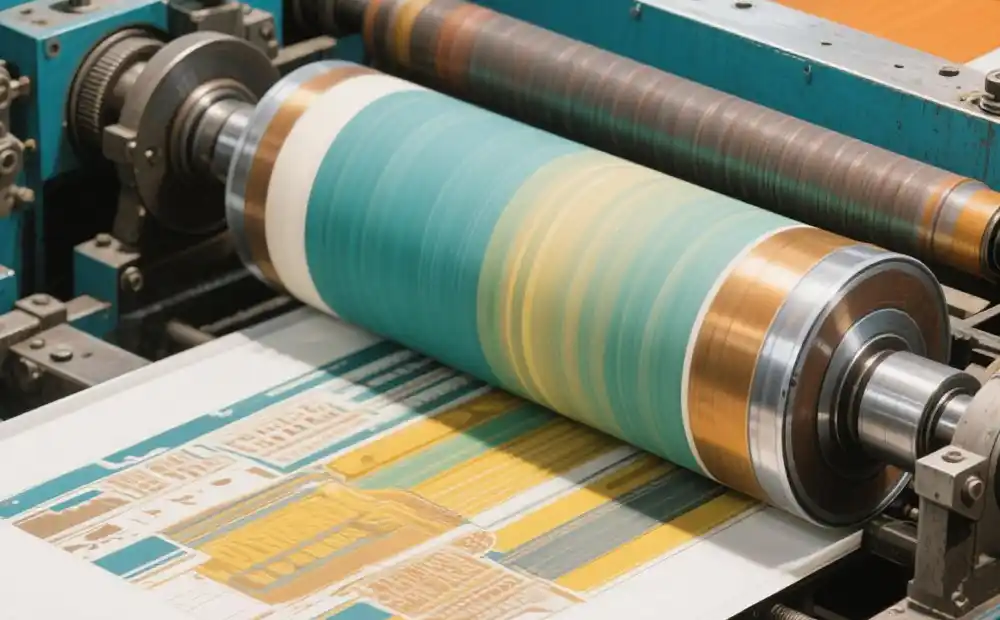
Take a printing enterprise in Shanghai, China, as an example. By adopting a combined cleaning solution of laser and ultrasonic cleaning for the cleaning of cigarette pack printing rolls, it has reduced the original cleaning time from 45 minutes to 18 minutes, significantly improving production efficiency while ensuring cleaning quality, providing a successful reference for the industry.