How Crosslinkable Resins Improve Chemical Resistance in Water-Based Inks
Date: Jul 14 2025 From: Star Color Views:
Introduction
Driven by global regulations on volatile organic compound (VOC) emissions and growing consumer demand for eco-friendly packaging, water-based inks have emerged as a critical component of sustainable printing solutions. Their applications span flexible packaging, labels, paperboard, and corrugated materials. However, the chemical resistance of water-based inks has long limited their use in high-performance scenarios: contact with alcohol, vegetable oils, alkaline detergents, or industrial solvents often causes ink film degradation, including swelling, color fading, or complete dissolution. This has forced manufacturers to rely on solvent-based or UV-curable inks for critical applications, despite their higher VOC emissions and printing costs.
To address these limitations, ink formulators are increasingly adopting crosslinked resins—advanced polymers that bridge the performance gap between water-based and solvent-based systems. By introducing controlled chemical crosslinking within the ink film, these resins enable water-based inks to withstand aggressive chemical exposure while retaining their eco-friendly properties, expanding their use into demanding fields such as pharmaceutical packaging, industrial labels, and food-contact materials.
What Are Crosslinked Resins?
Crosslinked resins are high-molecular-weight polymers with reactive functional groups on their side chains or end groups. These groups form covalent bonds (crosslinks) through two mechanisms: intramolecular reactions under specific conditions (self-crosslinking) or reactions with complementary crosslinking agents (external crosslinking).
Common Crosslinkable Functional Groups
- Hydroxyl groups (-OH): React readily with isocyanates, epoxies, or anhydrides to form urethane or ester bonds, offering high compatibility with acrylic and polyester backbones.
- Carboxyl groups (-COOH): Undergo esterification with hydroxyls or amidation with amines, typically requiring catalysts (e.g., organotin compounds) to accelerate reactions at moderate temperatures.
- Amino groups (-NH₂): React with epoxides to form β-hydroxyamines or with isocyanates to form urea bonds, exhibiting fast reaction kinetics even at room temperature.
- Epoxy groups (-epoxide): React with amines, carboxyls, or hydroxyls to form ether or ester bonds, known for high bond energy and chemical stability.
- Isocyanate groups (-NCO): Used in water-based systems in blocked forms (e.g., ketoxime or caprolactam-blocked) to prevent premature hydrolysis; deblock at 80–120°C and react with hydroxyls to form robust urethane crosslinks.
The Role of Crosslinking in Ink Films
Crosslinking transforms linear or lightly branched polymer chains in ink films into a three-dimensional network structure, fundamentally altering the material’s physicochemical properties. This network acts as a molecular barrier, restricting the penetration and diffusion of chemical agents. Specifically, crosslinking significantly enhances the following properties:
- Solvent and chemical resistance: The dense network reduces free volume within the polymer matrix, impeding the intrusion of solvent molecules that would otherwise cause swelling or dissolution.
- Mechanical durability: Interconnected polymer chains distribute stress more evenly, increasing tensile strength (typically 30–50% higher than non-crosslinked systems) and reducing elongation at break, minimizing cracking during substrate bending.
- Heat and abrasion resistance: The thermal stability of the 3D network resists high-temperature softening, while enhanced cohesion reduces particle detachment during friction.
- Water resistance: Restricted polymer chain movement lowers water absorption; crosslinked films typically exhibit a water contact angle > 85° (vs. < 60° for non-crosslinked films), preventing whitening or delamination in humid environments.
- Cohesive strength: Crosslinks reinforce intermolecular forces, preventing ink film tearing or transfer during lamination or processing.
Mechanisms of Crosslinked Resins in Water-Based Inks
Ambient or High-Temperature Drying
Self-crosslinking resins initiate crosslinking via intramolecular or intermolecular reactions during water evaporation. Reaction rates are moderate at ambient temperatures, while high-temperature drying (60–80°C) reduces crosslinking time to under 2 hours.
Addition of External Crosslinkers
Two-component systems mix resin dispersions with external crosslinkers just before use to avoid premature gelling. Common crosslinkers include:
- Aziridines: React with carboxyl groups at room temperature to form amine bonds, suitable for low-temperature applications like nonwoven printing.
- Polyisocyanates: Water-dispersible after blocking or hydrophilic modification, they react with hydroxyls at 40–60°C to form urethane crosslinks, delivering exceptional chemical resistance.
- Carbodiimides: React with carboxyl groups to form amide bonds, ideal for pH-sensitive systems where acid-base reactions must be avoided.
pH-Triggered Crosslinking
Resins stabilized at high pH via amine neutralization maintain water dispersibility through electrostatic repulsion between anionic chains. As the ink film dries, CO₂ absorption or acid migration from the substrate lowers the pH to 5–6, reducing charge density and prompting carboxyl groups to react with embedded crosslinkers (e.g., epoxy-functional nanoparticles). This mechanism ensures storage stability while enabling rapid curing during drying, making it ideal for non-absorbent substrates like PET or PP.
Starcolor’s Chemical-Resistant Water-Based Ink Solutions
Starcolor’s research focuses on synergizing resin chemistry with formulation engineering to overcome trade-offs between eco-friendliness and performance. Our crosslinking systems utilize advanced acrylic and polyurethane dispersions, optimizing reactivity and printability:
Chemical Resistance
Our acrylic-polyurethane hybrid resins, functionalized with hydroxyl and carboxyl groups, achieve > 90% gel content after curing. Per ASTM D5402-16 testing, they resist 70% ethanol, 50% IPA, and hand sanitizers without visible staining or delamination. For food-contact applications, we use crosslinkers compliant with FDA 21 CFR 175.300, ensuring safety in contact with edible oils or acidic foods.
Printability
Nanoscale resin particles (50–200nm) ensure low viscosity (< 1000cP at 25°C) for smooth transfer in flexographic or gravure printing. A custom surfactant system reduces surface tension to < 35mN/m, enabling excellent wetting on non-absorbent substrates like PE or aluminum foil.
Flexibility
Controlled crosslink density maintains 150–200% elongation, preventing cracking during bag-making or folding.
Versatility
We offer one-component self-crosslinking systems for high-speed label printing and two-component systems with polyisocyanate crosslinkers for industrial packaging, with custom formulations tailored to specific drying temperatures (40–120°C) and substrate types.
Typical Applications
- Pharmaceutical and cosmetic labels: Must withstand IPA or ethanol disinfection. Our two-component systems resist 100 cycles of 70% ethanol wiping without fading, meeting EU GMP cleanroom standards.
- Flexible food packaging: Pouches for snacks, edible oils, or sauces require resistance to fats and acidic contents. Our one-component self-crosslinking inks comply with EU 10/2011 and maintain integrity after 6 months of storage at 40°C/75% relative humidity.
- Nonwoven wipes and hygiene products: Labels on wet wipes or diapers must resist moisture and mild detergents. pH-triggered crosslinking ensures no delamination during storage or use.
- Overprint varnishes (OPVs): Used to enhance surface protection, our crosslinked OPVs resist solvent-based adhesives during lamination, preventing ink bleeding and ensuring adhesion strength > 5N/15mm per ASTM D3359.
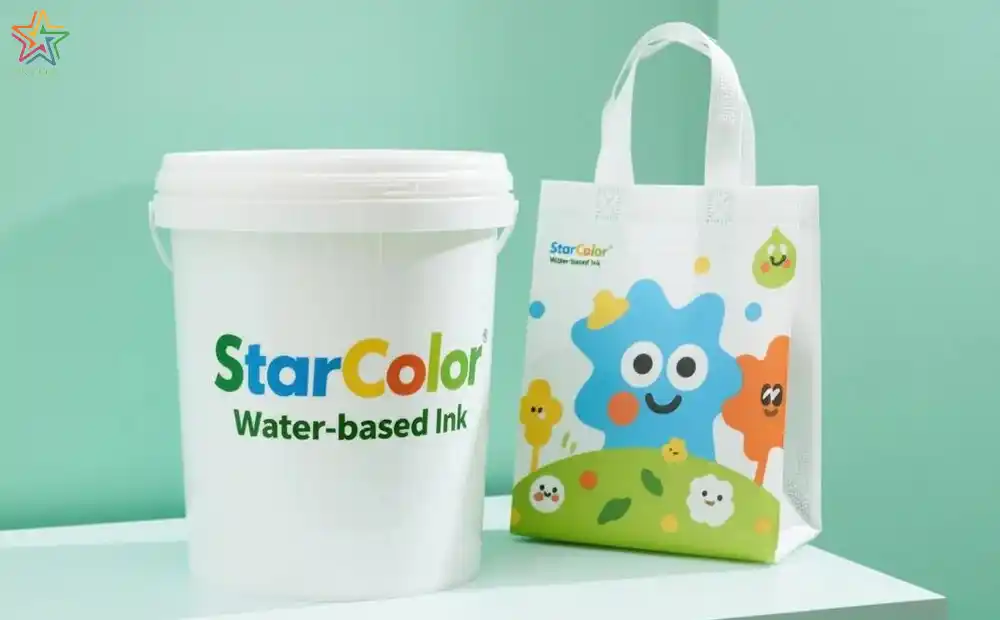
Conclusion
Crosslinked resins represent a paradigm shift in water-based ink technology, enabling eco-friendly systems to compete with solvent-based and UV-curable alternatives in high-performance applications. By designing controlled crosslinking reactions—whether self-activated, externally crosslinked, or pH-triggered—formulators can tailor ink films to resist harsh chemicals, mechanical stress, and environmental factors while maintaining low VOC emissions and regulatory compliance.
Starcolor is committed to innovating crosslinked resin systems that balance performance, processability, and sustainability. As industries increasingly prioritize both functionality and environmental responsibility, the applications of crosslinked water-based inks will continue to expand, demonstrating that eco-friendly solutions need not compromise durability.