How to increase the adhesion of water-based ink on non-woven fabric?
Date: Jan 24 2025 From: Star Color Views:
With the increasing awareness of environmental protection, the application of flexographic water-based ink in non-woven printing is becoming increasingly widespread. However, the problem of insufficient adhesion of water-based ink on non-woven fabrics seriously affects the printing quality and practicality of products. Solving this problem is of great significance for promoting the development of flexographic water-based ink in the field of non-woven printing.
Characteristic analysis of flexographic water-based ink and non-woven fabric
Characteristics of flexographic water-based inkFlexographic water-based ink uses water as a solvent, which has the advantages of environmental protection and low VOC emissions. But its main components are water-based resins, pigments, additives, etc. Compared with traditional solvent based inks, there are differences in chemical structure and physical properties. The film-forming characteristics of water-based resins and their ability to encapsulate pigments, as well as the type and amount of additives, all affect the overall performance of ink, especially its adhesion on non-woven fabrics.
Characteristics of non-woven fabricNon woven fabric is a type of non-woven fabric made by combining oriented or randomly arranged fibers through friction, interlocking, or bonding, or a combination of these methods. Its fiber structure is loose and its surface energy is low, which makes it difficult for water-based ink to adhere well to its surface. Meanwhile, non-woven fabrics come in a variety of materials, such as polypropylene (PP), polyester (PET), etc. The chemical properties and surface characteristics of different materials also vary, further increasing the difficulty of ink adhesion.
Analysis of Reasons for Insufficient Adhesion
Ink formula factorsImproper selection of water-based resins: Some water-based resins have poor chemical compatibility with the surface of non-woven fabrics, making it difficult to form effective chemical bonds or physical adsorption, resulting in poor adhesion. For example, some universal water-based acrylic resins have insufficient affinity for PP non-woven fabrics with low polarity.
Unreasonable use of additives: Additives play an important role in ink, but if the amount or types of dispersants, leveling agents, and other additives are too large or inappropriate, they may migrate to the surface of the ink, affecting the adhesion between the ink and non-woven fabric.
Surface properties of non-woven fabricLow surface energy: The surface energy of most non-woven fabrics is lower than the surface tension of ink, making it difficult for ink to spread and adhere on the surface of non-woven fabrics, easily forming water droplets and unable to come into close contact with non-woven fabrics.
Surface impurities and residual release agents: During the production process of non-woven fabrics, some impurities or release agents may remain, which can hinder direct contact between ink and non-woven fabric surface and reduce adhesion.
Printing process issues
Insufficient printing pressure: During flexographic printing, if the printing pressure is not sufficient, the ink cannot be fully transferred to the surface of the non-woven fabric, and cannot be tightly adhered to the non-woven fabric, resulting in a decrease in adhesion.
Inappropriate drying conditions: If the drying speed is too fast, the moisture in the ink will evaporate rapidly, which may cause the ink to solidify before fully penetrating and adhering, affecting adhesion; If the drying speed is too slow, it may cause ink to migrate or flow during the drying process, which also reduces adhesion.
Strategies for addressing adhesion issues
Optimize ink formulaChoose the appropriate water-based resin: Based on the material of the non-woven fabric, choose a water-based resin with good chemical compatibility. For example, for PP non-woven fabric, modified acrylic resin containing special functional groups (such as hydroxyl, carboxyl, etc.) can be used. These functional groups can react chemically with the molecules on the surface of PP to form chemical bonds and improve adhesion.
Reasonably adjust additives: precisely control the dosage and type of additives. Reduce the amount of additives that may affect adhesion, such as reducing the addition of leveling agents appropriately. At the same time, adding adhesion promoters, such as additives containing active groups such as epoxy and amino groups, can form bridges between ink and non-woven fabric, enhancing their bonding strength.
Processing the surface of non-woven fabricCorona treatment: Through corona discharge, the molecular structure of non-woven fabric surface changes, increasing surface polarity and roughness, improving surface energy, and thus improving ink adhesion. The strength and duration of corona treatment need to be adjusted according to the material and thickness of the non-woven fabric. Generally speaking, a high treatment strength may damage the non-woven fabric, while a low treatment strength may not achieve the expected treatment effect.
Plasma treatment: Using plasma to undergo physical and chemical reactions with the surface of non-woven fabric, introducing active functional groups, removing surface impurities and residual release agents, and improving the wettability and adhesion of the surface. Plasma treatment has the advantages of uniform treatment effect and no pollution, but the equipment cost is relatively high.
Improve printing technologyAdjust printing pressure: Determine the optimal printing pressure through experiments to ensure that the ink can be fully transferred to the surface of the non-woven fabric and tightly adhered to it. Generally speaking, for non-woven fabrics with softer texture, the printing pressure can be appropriately reduced to avoid damaging the non-woven fabric; For non-woven fabrics with a harder texture, the printing pressure can be appropriately increased.
Optimize drying conditions: Select the appropriate drying method and parameters based on the characteristics of the ink and the material of the non-woven fabric. When using hot air drying, it is necessary to control the temperature and speed of the hot air, so that the moisture in the ink can evaporate evenly and slowly, ensuring that the ink has enough time to penetrate and adhere to the surface of the non-woven fabric during the drying process. At the same time, a segmented drying method can be used, where low-temperature pre drying is performed first to preliminarily solidify the ink, followed by high-temperature drying to complete the thorough solidification of the ink.
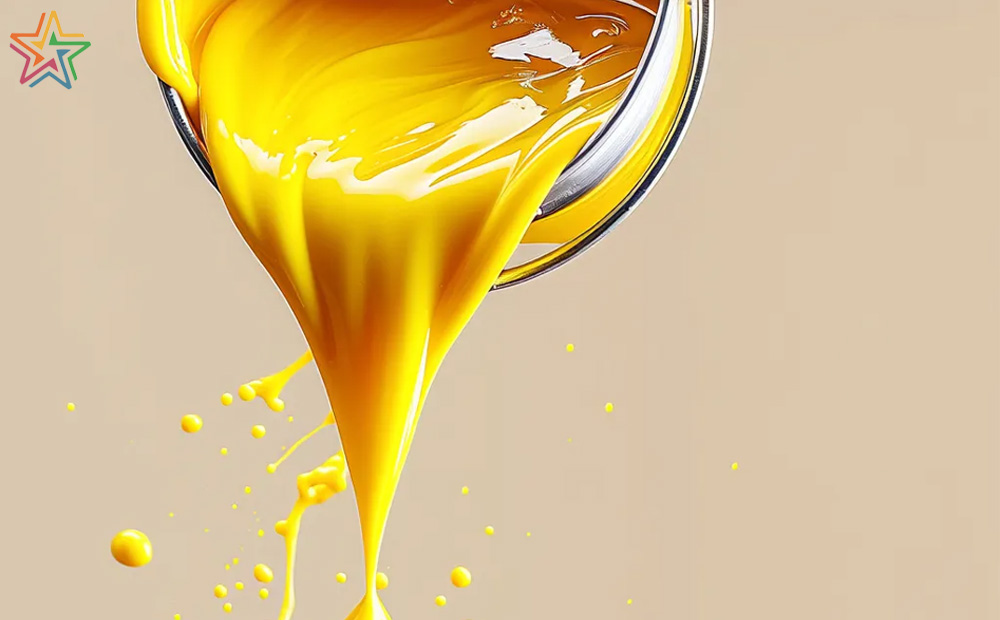
To solve the problem of insufficient adhesion of flexographic water-based ink on non-woven fabrics, it is necessary to start from multiple aspects such as ink formula optimization, non-woven fabric surface treatment, and printing process improvement. By selecting appropriate water-based resins and additives, effectively surface treating non-woven fabrics, and optimizing printing process parameters, the adhesion of water-based inks on non-woven fabrics can be significantly improved, printing quality can be enhanced, and the widespread application of flexographic water-based inks in the field of non-woven printing can be promoted.